SpotがBMWグループ工場でイノベーションを促進
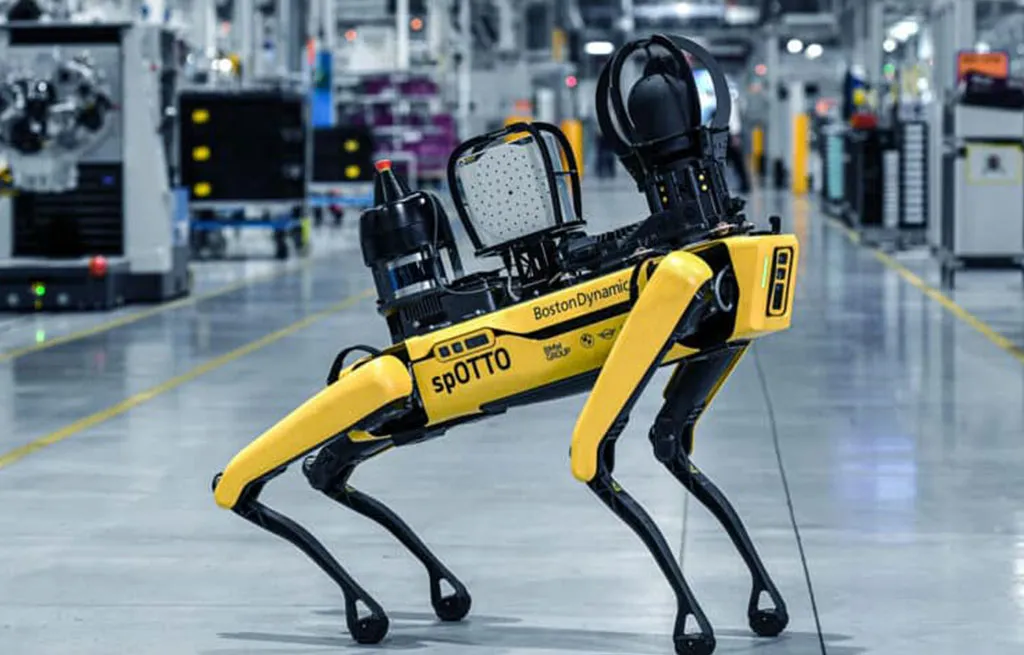
2023年イギリス「スマート・ファクトリー・オブ・ザ・イヤー」に選ばれたBMWグループハムズ・ホール工場は、集中管理されたデータを利用して効率を最大化しています。
BMWグループのハムスホール工場では、世界的に有名なエンジンやコンポーネントを組み立てる過程で、膨大な量のデータが生成されます。しかし、そのデータを理解することは、パズルのピースの山を整理するような煩雑さがありました。
イギリスバーミンガム近郊に位置するハムズホールは、主要なエンジン部品を加工し、BMWグループのさまざまな車種向けに、高効率の3気筒および4気筒ガソリンエンジン、さらにはV8およびV12エンジンの組み立てを行っています。施設内では膨大なデータが収集されていますが、重要なデータが個別に管理されてしまい、ハムズ・ホール全体のオペレーションを俯瞰的に把握することが困難でした。
2年前、ハムスホールはデータ収集インフラ全体を一元化する取り組みを始めました。まず施設の完全接続型デジタル・ツインを開発し、その後2023年にボストン・ダイナミクス社の四足歩行ロボットSpot®を導入して、このデジタル・ツインに直接データをフィードバックする自動検査を実施しました。
その努力により、ハムスホールはイギリスで最も権威のある業界賞である2023年Manufacturer MX賞で「スマート・ファクトリー・オブ・ザ・イヤー」の栄誉に輝きました。
ハムズ・ホールの イノベーション&デジタル化(I&D)チーム の 技術リードであるブラッド・トムリンソン 氏は「私たちは競争力を維持し、これらの部品を供給する上で信頼できる存在でなければなりません。施設内の全員が、このイノベーションを活用できることを理解し、開発されたツールをどのように使えば自分たちの担当エリアを改善できるのかを考えるべきです。」と語ります。
大量のデータストリームを一か所へ
ハムズ・ホール工場では、 週を通じて複数のシフト体制のもと、3つの加工ラインで大量生産を行っています。 これにより、年間約140万個の部品 が製造され、2つのエンジン製造施設では年間約40万基のエンジンが生産されています。かつて社内チームは、それぞれの担当分野に関連するデータをまとめるために、400以上のカスタムダッシュボード を使用しており、データのアクセス方法もバラバラ でした。そのため、ハムズ・ホールには、すべてのチームメンバーがアクセスできる「信頼性の高い唯一のデータ基盤」 が必要だったのです。
デジタル・ツインの構築には、15以上の異なるITシステムを統合し、スマートフォンやタブレットでアクセスできる工場の3次元モデルを作成する必要がありました。これは非常に困難な作業でしたが、I&Dチームは、長期間にわたって機能し、従業員が簡単に受け入れられる仕組みを作ることに全力を注ぎました。その結果、デジタルツインは現在、リアルタイムで生産データを表示し、工場内の各システムの状態を緑や赤のアイコンで識別しやすくなりました。
イノベーション&デジタル化チーム(I&D) のマネージャーである クリスチャン・ポス 氏は「デジタルツインをノーコードプラットフォームとして活用することで、このダッシュボードの乱立した状況を整理したいと考えました。」と語ります。
「私たちは、すべてのデータを従業員や専門家向けに整理し、利用できる状態にしました。それにより、何か問題が発生したときに、適切なデータソースを探し出す時間を省くことができるようになり、すぐに問題に対応できるようになったのです。今では、誰もがデジタルツインを参照するようになっています。」と述べます。
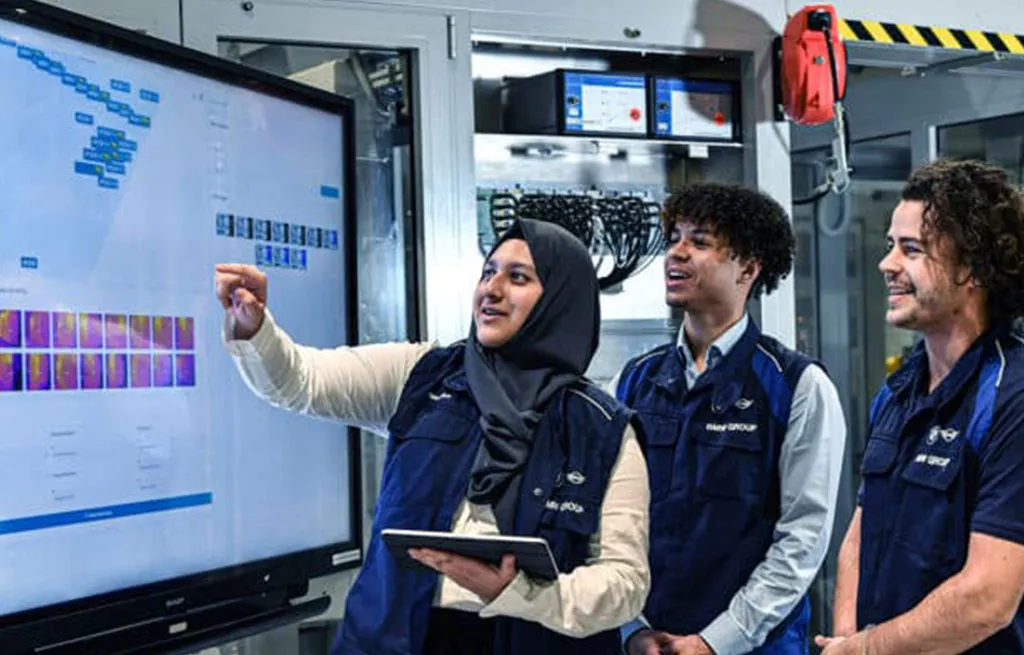
検査の拡大
BMWによれば、生産を維持するために必要な機械の量は膨大であり、定期的な検査によって機器が常に正常に作動していることを確認する必要があります。ハムスホールには、空気漏れのリスクにさらされやすい配管、冷凍機、油圧パネルなどを備えた大規模なトンネルシステムがあり、この設備は重要な役割を担っているにもかかわらず、デジタルツインによって、施設内に点検データがまったく存在しないエリアがあることが明らかになりました。これにより、イノベーション&デジタル化(I&D)チームが、メンテナンス作業員の検査作業の拡大と、自動化を支援する必要があることが明らかになったのです。
「熟練した専門家でも、手作業での点検には1回のシフトにつき数時間かかることがあります。 チームの時間を予防保全の作業に再活用できれば、当然ながら、より効率的に運用できるようになります。」
ーブラッド・トムリンソン、ハムズ・ホール革新・デジタル化チーム、テクニカル・リード
「BMWではあらゆるデータシステムを導入していますが、それでもまだ死角がたくさんあることがわかりました」とポス氏は語ります。以前は、工場は業者に依頼して専門機器を使って空気漏れの検査を行っていましたが、ハムズ・ホールのメンテナンス・チームがこれらの手作業による点検を引き継ぐことは、必要なメンテナンスや修理に費やす時間が奪われることに繋がります。そこでI&Dチームは、オートメーション化に目を向けました。
「熟練した専門家でも、手作業での点検には1回のシフトにつき数時間かかることがあります。 チームの時間を予防保全の作業に再活用できれば、当然ながら、より効率的に運用できるようになるのです。予防保全のためにチームの時間を再利用できれば、当然、効率は上がります。」とトムリンソン氏は語ります。
固定センサー vs 可動センサー
自動測定値を収集する1つの選択肢として、IoTセンサーを機器に設置することも検討されましたが、I&Dチームは、必要なセンサーをすべて設置するには何年もかかり、コストがかかりすぎると判断しました。その一方で、IoTセンサーを搭載し、同じ範囲を常に網羅しながら、厳しい環境下でも正確な測定を繰り返すことができる移動型のロボットであれば、コストは数分の一で済むと考えました。その課題を解決することができたのが、ボストン・ダイナミクス社のSpotロボットだったのです。
「現在、私たちの生産データは非常に高い透明性を確保できていることを実感しています。この透明性を活かして、まずはデータの抜けている部分を特定し、Spotを使ってそれを補いたいと考えたのです。その結果、 施設全体の温度データや、手動ダイヤルの読み取り値、音響異常の詳細な情報が取得しきれていないことが発覚しました。Spotは、まさにそうしたデータを補うために活用しています。」
とトムリンソン氏は述べました。
若い人材による事業拡大
Spotのもうひとつの利点は、操作に長年の経験を必要としないことです。BMWには大学生を対象とした大規模なインターンシップ・プログラムがあるため、これは特に重要なポイントでした。イギリスでは、学部生が 3年次の1年間を専門性の高いインターンシップに専念する仕組みになっていて、BMWではインターン達を社員と対等な立場として扱っています
しかし、インターンは毎年入れ替わるため、BMWハムズ・ホール工場では、新しい技術に素早く適応できるインターン生が求められていました。 Spotの導入により、I&Dチームは点検作業を拡張しながら新たなソリューションの開発を進め、インターンシップの質も確保できるようになったのです。
実際、Spotの統合プログラムは 2人のインターンが主導 しています。
「私たちは若手のプロフェッショナルのチームと協力することで、新しい技術の展開を迅速に進められています。 さらに、学生にとって素晴らしいインターンシップの機会を提供できるだけでなく、既存のハードウェアがいかに柔軟であるかを示す証拠にもなっています。」とトムリンソン氏は述べた。
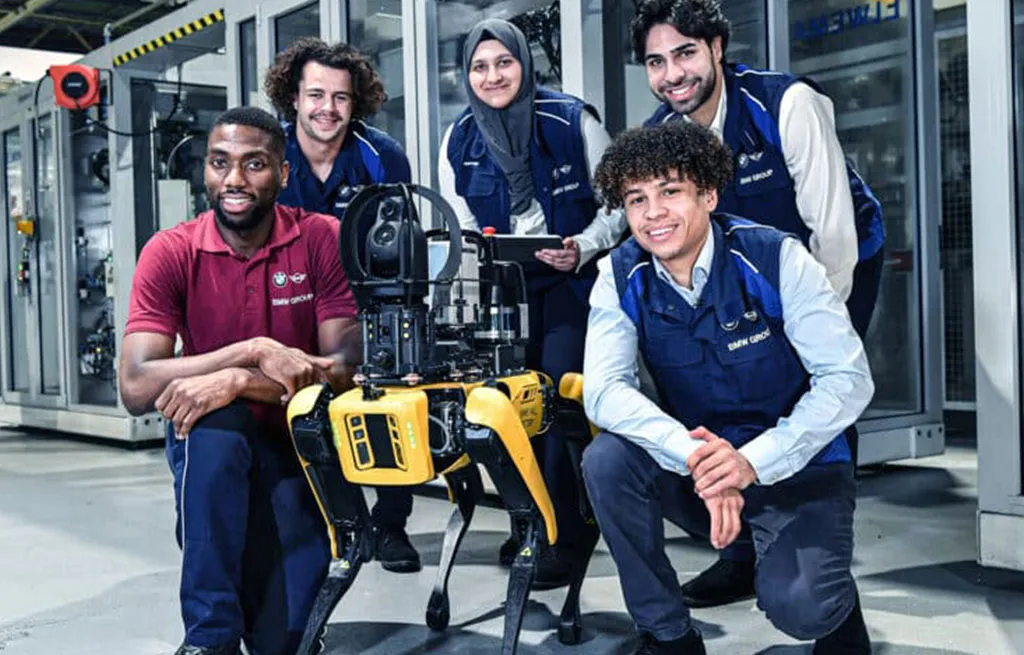
機械は故障してはならない
例えば、データ分析学を専門とするインターンは、Spotの自律的なルートのプログラミングを担当し、Spotのデータをデジタルツインに統合することを監督している。インターン生が、Spotが1日に6回自律歩行するようにプログラムし、そのルートは重要度の高い順に決定されます。
Spotでは現在、温度測定用のサーモグラフィ、空気漏れを特定するためのフルークSV600音響センサー、360°カメラ、3Dスキャン用のLIDARなど、複数のセンサーを検査に使用しています。これらの機械は24時間365日稼働させなければならないため、自動歩行の優先順位があり、あるステーションは1日1回、別のステーションは1週間に1回検査するスケジュールが作成されます。
ポス氏いわく、音響センサーを使った最初の数週間の検査で、Spotが予期せぬ場所で空気漏れを発見したため、工場現場のチームメンバーが関心を持ち、定期的に監視するようになったといいます。
「Spotからデジタルツインへ、そしてメンテナンス担当者のいる工場現場へと、業務サイクルが確立されたと言えるでしょう。Spotは、ほぼ完全にメンテナンス・システムに組み込まれたといえるでしょう。」
Spotのデータは3Dへ
トムリンソン氏は、四足歩行ロボットが業務の効率化に貢献している完璧な例 として、保守作業のリクエスト が挙げられると語ります。従業員はデジタル・ツインにログインし、端末上で特定のエリアを拡大し、遠隔でメンテナンスのリクエストを送信できるようになったのです。
トムリンソン氏は「Spotからデジタルツインへ、そしてメンテナンス担当者のいる工場現場へと、業務サイクルが確立されたと言えるでしょう。Spotは、ほぼ完全にメンテナンス・システムに組み込まれたといえるでしょう。」と語ります。
新たなユースケース
Spotの稼働時間の 80% は 定期点検 に充てられますが、残りの20% は 未来を見据えた活動に充てられています。
産業工学を専門とするインターンは、変革管理とSpot活用の拡大に重点を置いており、工場の現場で同僚と対話しながら、Spotが提供できる革新的なソリューションを見つけ出す役割を担っています。
「それが点検であれ、異常検知であれ、保守部品の管理であれ、現場の人々がSpotを目にしたときに感じるのは、純粋な興奮です。」と、ポス 氏は述べました。
実習生はタブレットでSpotを操作し、生産ラインにロボットを持ち込んで臨機応変に検査することができます。長年の経験があり、自社の装置を熟知している従業員は、ベアリングの緩みや異常な振動を調査するためにSpotを使用することが可能です。実習生がSpotを用いて計測を行い、チームは修理が緊急性の高いものか、修理まで多少の猶予があるかを判断することができるのです。
ポス氏は「我が社の社員はSpotを最先端の技術として捉えており、ロボットが動き回ってあらゆるものを点検する姿はとてもクールだと感じています。その一方でSpotが工場の現場にいることで生まれる人々の温かな反応や、コミュニケーションこそが重要なのです。それらを通して、更に 部門間の協力が生まれ、Spotが提供する価値を実感することができるのです」と述べました。